Coating & Laminating Adhesive Application Technologies - Industry Solutions
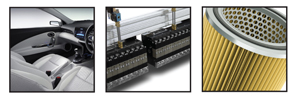
If the conventional solution outperforms every other technology, then conventional is fine. But here’s the problem: that’s not usually the case. Our customers tell us that there are major downsides to all conventional adhesive application methods, including roll coating, scatter coating, needle-punching, flame laminating and ultrasonic. They are inefficient, costly, and some even require extreme preventative measures to avoid environmental damage.
That’s exactly the kind of challenge we like and the reason why ITW Dynatec keeps listening, learning and creating industry-changing technology, like our slot die and UFD (Unified Fiber Deposition) application systems. We expand the boundaries of conventional technology in order to bring our customers eco-friendly solutions that exceed their needs and increase efficiencies, saving time and money.
Today, we’re moving the coating and lamination industry forward with our UFD Omega™ and Random Fiber spray technologies. Whether you're joining nonwoven to nonwoven, film to nonwoven, or film to film, laminated products require precision adhesive add-on accuracy in the machine and cross web direction. ITW Dynatec's segmented and metered UFD applicators provide unmatched precision add-on levels and pattern accuracy as well as adhesive and cost savings.
Why Hotmelt?
- Go green. Most hot melts are totally biodegradable and make your products totally recyclable. They also create no VOCs (solvent emissions), no waste water issues and no airborne contaminants, making EPA issues a thing of the past.
- Save adhesive, increase profits. Offering lighter coat weights, hot melt adhesives mean you can use less adhesive and save more money.
- Make more product (correctly). Not only do hot melts offer high-precision adhesive application at faster production speeds, they can also be processed immediately after adhesive application, saving time and space in your facility.
- Add value with additives. Both hot melt adhesives and ITW Dynatec’s technologies are compatible with various value-adding additives, including anti-microbial, flame retardant, anti-oxidant, UV inhibiting and water repelling chemicals.
Hot Melt Polymer Advantages |
Mechanical Advantages |
- Make your product more "green"
- Most are totally biodegradable
- No VOC's (solvent emissions)
- No waste water issues
- No airborne contaminants
- Products totally recyclable
- Lighter coat weights
- Faster production speeds
- Immediate post processing
- Energy savings
- Alleviate EPA issues
- Ability to support various additives such as:
- Anti-Microbial
- Flame Retardants
- Anti-Oxidants
- UV Inhibitors
- Water Repellant
|
- Variable coat weights on the fly
- Faster production speeds
- Intermittent patterning
- Vary web widths on the fly
- Less overall cost
- Line speeds exceeding 2500 ft/min.
- No burn through of thin substrates
- Non contact - will not compress or crush the substrate
- Provide measured breathability for filter production
- Monitor and compensate for variances in line speed to maintain constant coat weight
- Used in single layer and multiple layer laminating applications.
|
Innovation is not just about creativity or ingenuity. It’s also about listening. ITW Dynatec knows that creating effective solutions is a two-part process: we ask our customers what they need and then we create technology that far exceeds those needs. The disposable hygiene industry is an excellent example. Drawing on four decades of experience, ITW Dynatec has continuously pushed adhesive and fluid dispensing technology into the next generation for disposable hygiene products.
- Technical Textiles - Coating and/or lamination is the preferred method of adhering substrates together in the technical textile industry, but conventional technologies are inefficient and often unsafe for both the operator and the environment. At ITW Dynatec, we think unsafe and inefficient are simply unacceptable.
- Nonwovens Applications - For applications requiring a solid barrier or coating on a nonwoven substrate, ITW Dynatec’s Apex slot die technology delivers exceptional results, while UFD fiberized spray allows customers to create a product with flow characteristics between two composites.
- Tape & Label - The wide range of capabilities offered by ITW Dynatec’s technologies, including compatibility with a wide range of substrates, adhesives, speeds, widths and coat weights, open up a remarkable range of options for tape manufacturers. From one-inch-wide paint tape to sixty inch master rolls, with a .5 ml to 10 ml coating, tape of all kinds is made possible by ITW Dynatec technology.
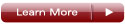
Solution-Based Technology
UFD Fiberized Spray Technology
- Modular applicators can be combined to build segmented applicators from one to as many as 200 ports.
- The industry's most precise applicator for size and placement of multiple fiber size patterns.
- Laminated plate technology (LPT) produces monofilament strands of adhesive and uses heated air to elongate those strands and lay them down in random or ordered patterns.
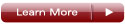
Slot Applicator Technology
- Allows for custom designs and offers multiple hose feed for precision patterns to each adhesive pattern, delivering precision for continuous or high-speed intermittent capability.
- Utilizes extreme high-speed module technology and Eagle Beak die lip technology to provide the best quality intermittent applications and long life.
- Non-Contact, highly accurate slot applicators for wide web coating and lamination. Perfect for applications where the substrate is heat sensitive and a perfect finish is required.
Adhesive Supply Units
- Up to 1,600 lb hopper capacity
- Pump output rate of up to 1400 lbs/hr for ultimate performance.
- Patented Melt-On-Demand no char system equipped
- Multiple grid rows for superior melt rate.
Getting Ahead with Superior Technology
- ITW Dynatec’s coating and laminating technologies deliver an industry-leading set of advantages:
- Vary coat weights and web widths on the fly
- Produce at faster speeds
- Use intermittent patterning
- Reduce costs
- Increase line speeds up to and above 2500 ft/min.
- Eliminate burn-through of thin substrates
- Protect substrates with non-contact technology, which will not compress or crush the substrate
- Provide measured breathability for filter production
- Monitor and compensate for variances in line speed to maintain constant coat weight
- Use in single layer and multiple layer laminating applications